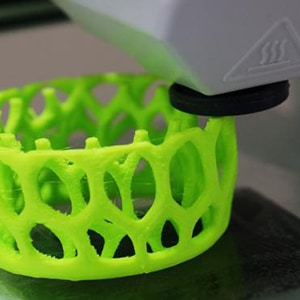
Récemment, des étudiants américains ont créé un haut-parleur en l’imprimant intégralement en trois dimensions. Depuis leur commercialisation, les imprimantes 3D grand public servent principalement à reproduire des objets relativement simples, comme la coque d’un smartphone ou la tête de Dark Vador.
En créant un objet beaucoup plus composé en volume, ces étudiants ont démontré l’intérêt que ce type de technologie pourrait avoir pour l’économie, notamment pour l’industrie. Il est vrai que le haut-parleur qu’ils ont créé est assez grossier et n’a pas des qualités sonores extraordinaires, mais il fonctionne. Et tout a été réalisé en 3D !
Vers une nouvelle révolution industrielle ?
Cette prouesse est due à l’utilisation d’encre à nanoparticules d’argent déposée pour former la bobine, tandis que l’aimant a été conçu avec de l’encre composée de ferrite de strontium et d’un polymère. Le résultat laisse penser que, dans le futur, des produits manufacturés complexes pourraient être produits en série en impression 3D. Elle présente l’énorme avantage de n’utiliser que la quantité de matière nécessaire à la fabrication d’une pièce, à l’inverse des méthodes habituelles de soustraction, comme le fraisage, qui en rejette énormément. Moins coûteuse, assez rapide, cette technologie fait actuellement l’objet d’intenses recherches.
L’idée d’imprimer en 3D n’est pas neuve. Le premier à l’avoir eue est l’écrivain de science-fiction Arthur C. Clarke. En 1964, dans une émission de la BBC, il imagine un Répilicator, une machine pouvant reproduire tous les objets. Ce concept devient un peu réalité en 1984 avec le dépôt du brevet de la stéréolithographie. Ce procédé, qui consistait à durcir une résine en l’exposant à des rayons lumineux, est l’ancêtre de l’impression en 3D. Cette découverte est attribuée à Charles W. Hull, aujourd’hui à la tête du groupe 3D Systems, un des leaders sur le marché de la fabrication additive. On leur doit notamment le format de fichier informatique .stl qui est compatible avec toutes les imprimantes 3D.
Il existe aujourd’hui de nombreuses manières d’imprimer en volume. La plus utilisée semble être la Fused Deposition Modeling (FDM) qui consiste à déposer un matériau couche par couche. Elle implique qu’un objet soit modélisé numériquement grâce à un logiciel de conception assistée par ordinateur (CAO), puis que le fichier soit envoyé vers un imprimante qui découpe le modèle en tranches et le recréer par le dépôt de couches successives. La matière utilisée la plus courante est le plastique, mais il est possible de modéliser avec de la céramique, des métaux, de la résine, du bois, du nylon, du sucre, et même avec des matières organiques. Du coup, ce procédé intéresse de nombreux secteurs d’activités.
L’impression 3D bientôt dans l’espace
Pour Barack Obama, il ne fait pas de doute que l’impression 3D peut révolutionner notre façon de produire des objets. En février 2013, lors de son discours sur l’état de l’Union, le président américain a déclaré vouloir développer les centres d’impression 3D. Le potentiel est tel, d’après lui, que cela pourrait avoir des conséquences économiques majeures, particulièrement sur l’emploi. L’impression 3D pourrait notamment permettre de relocaliser la production d’objets manufacturés dans les pays riches, alors qu’aujourd’hui l’Asie est l’atelier de la planète. En France, le ministère du Redressement productif s’y intéresse également de près. Les plus optimistes pensent que nous sommes à l’aube d’une nouvelle révolution industrielle.
Dans l’aéronautique, la Nasa a déjà annoncé son intention d’envoyer une imprimante 3D sur la station internationale (ISS) à l’automne prochain. Elle permettra de produire en apesanteur 30 % des pièces de rechange dont les astronautes ont régulièrement besoin. L’agence spatiale américaine a également testé un moteur d’avion dont l’injecteur a été fabriqué en volume. Elle parle même d’imprimer la nourriture en 3D pour les astronautes en longs séjours dans l’espace.
Mais ces innovations ne se limitent pas l’industrie. En médecine, les imprimantes 3D sont également en train de révolutionner la fabrication de prothèses. Outre-Atlantique, un homme a reçu un implant sur mesure en remplacement de 75 % de son propre crâne.